El Dorado Hills, Calif.-based McClone Construction Co. used the project management and analytics platform to transition from traditional methods (paper and Microsoft Excel) to advanced, intelligent resource management. Founded in 1975, McClone specializes in structural concrete and concrete formwork and has completed well over 1,200 projects across the United States, with offices in California, Washington, Hawaii, Colorado and Texas.
Published July 28, 2022 . 10 mins read
McClone Construction
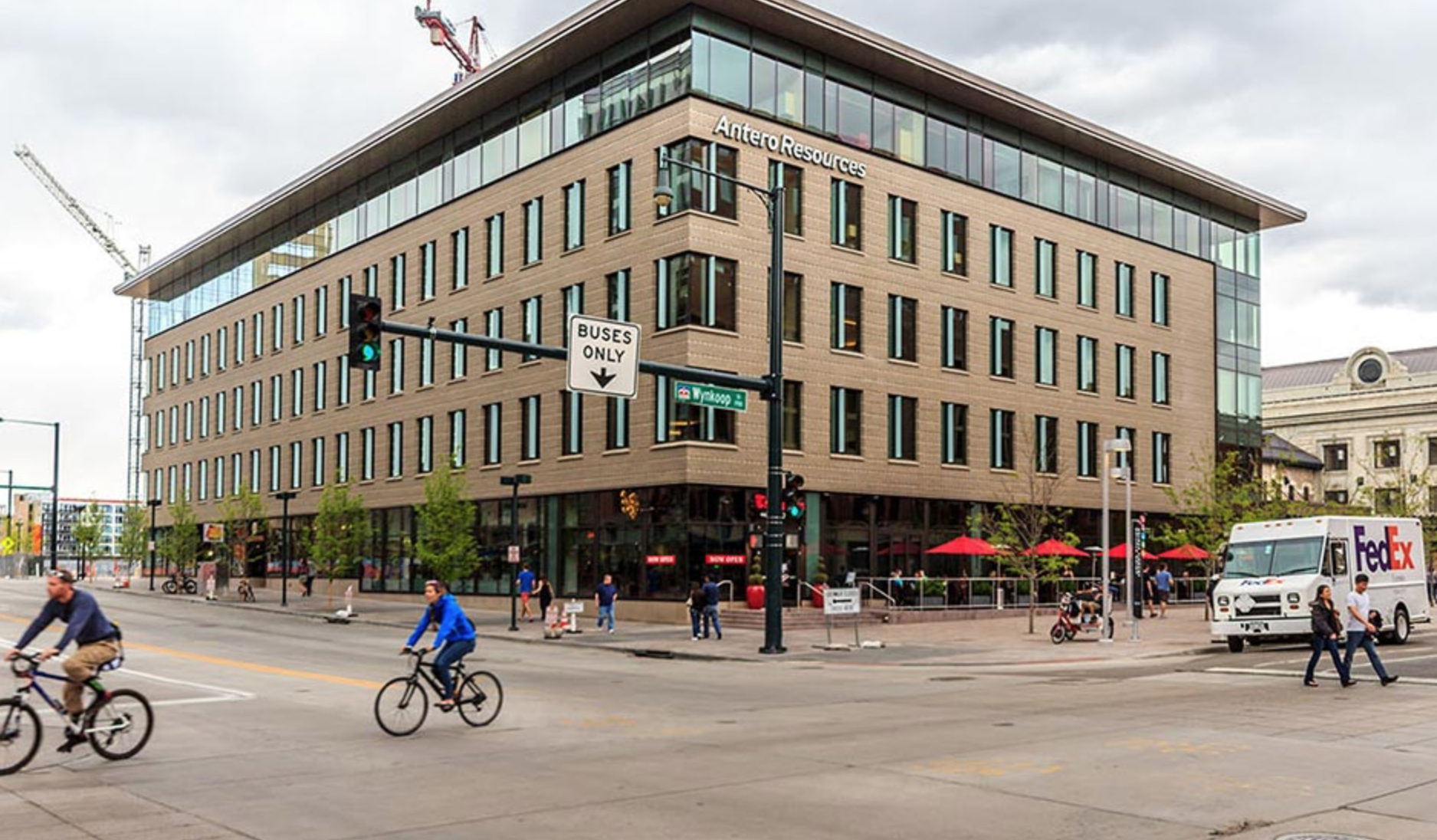
About 100 McClone team members, including PMs, superintendents, engineers, estimators and c-suite executives, now use ProNovos resource-management tools. McClone began rolling out the platform in 2018 and has managed more than 200 projects in the system. The subcontractor also leverages ProNovos to better determine which projects to target for bids. “As a result of our experience with this platform, we’re now big believers in intelligent resource management,” said Mikeal Kanouff, Texas Area Manager for McClone.
“
As a result of our experience with this platform, we’re now big believers in intelligent resource management.
Mikeal Kanouff
Area Manager, McClone
“
As a result of our experience with this platform, we’re now big believers in intelligent resource management.
Mikeal Kanouff
Area Manager, McClone
INTELLIGENT RESOURCE MANAGEMENT: THE BIG PICTURE
McClone previously relied on the approach used by most contractors seeking to track and manage projects, personnel and equipment: using paper records (such as safety forms), typing data into static spreadsheets, and endlessly emailing photos, drawings and RFIs.
Like many of today’s subs, McClone was also using more and more construction apps, a situation that was on the verge of creating some problems. “Busy construction professionals don’t have time to master four to six different pieces of software, all opened and closed separately, and all with different logins and passwords,” Kanouff explained. ProNovos, by contrast, integrates multiple streams of resource and project-planning data into a single, cloud-based interface. The dashboards are accessible from any location or device.
“It’s huge to be able to go in and know, without jumping systems, what your equipment and personnel needs are or what RFIs are hanging out there, all in one spot,” Kanouff said. For example, a project manager using the platform to review drawings might realize that a certain piece of concrete-forming equipment will be needed. “Without leaving ProNovos, that person can jump right over to the equipment section, see where that item is located and where it’s going, and then use that information to plan for the job,” Kanouff said. “Integration makes a very big difference.”
“
Busy construction professionals don’t have time to master four to six different pieces of software, all opened and closed separately, and all with different logins and passwords.
Mikeal Kanouff
Area Manager, McClone
“
Busy construction professionals don’t have time to master four to six different pieces of software, all opened and closed separately, and all with different logins and passwords.
Mikeal Kanouff
Area Manager, McClone

CUSTOM FORMS
One of the subcontractor’s final steps in “going paperless” came in 2021 with McClone’s company-wide adoption of ProNovos’ custom form-builder module.
Across the industry, many subs either print and scan paper forms or work with writable PDFs for safety, inspection, waiver and other forms. To be sure, writable PDFs eliminate the need to decipher handwriting or for the superintendent to physically distribute paper copies by crisscrossing the jobsite with a clipboard in hand. Nonetheless, writable PDFs have some distinct disadvantages as well. For example, they cannot be written back to a database.
The ProNovos form-builder allows subs to create all kinds of custom forms just by dragging and dropping different elements. Moreover, the form data collected by the system is ready for analysis, now and in the future. “You can look up and inspect anything on the form and track historical trends,” Kanouff said. McClone, for example, uses ProNovos to track how frequently different topics are covered during weekly safety meetings (the weekly meetings form includes a check box for which topics were covered). “Running analytics helps you make sure you don’t skip anything important,” Kanouff said. “You can just run your report and see where you are with that material.”
Likewise, subs can use ProNovos analytics to bend the curve downward on lost-time incidents and injuries, near misses, or violations related to the likes of PPE, fall-protection, scaffolding, lockout/tagout or hazard communication. That’s because the ProNovos form-builder allows them to track this kind of information over time for the entire company, by project and by superintendent—something you can’t do with a static PDF.
McClone has been using ProNovos’ custom form-builder for 95 percent of its former paperwork. Prior to that, there was a higher likelihood of personnel forgetting to fill out forms or leaving important printouts in gang boxes or truck cabs. “Now you take out your iPad out, click to sign it, hit the email button and put your iPad away,” Kanouff said.
The calendar view allows the company to see precisely what paperwork was completed and when. “That’s a big one, because we have forms that are due weekly,” Kanouff said. “So instead of going back and trying to look in a file folder to make sure that everything was done on certain dates, you can just look at the calendar view in ProNovos to see if anything is missing.”
“
Running analytics helps you make sure you don’t skip anything important. You can just run your report and see where you are with that material.
Mikeal Kanouff
Area Manager, McClone
“
Running analytics helps you make sure you don’t skip anything important. You can just run your report and see where you are with that material.
Mikeal Kanouff
Area Manager, McClone
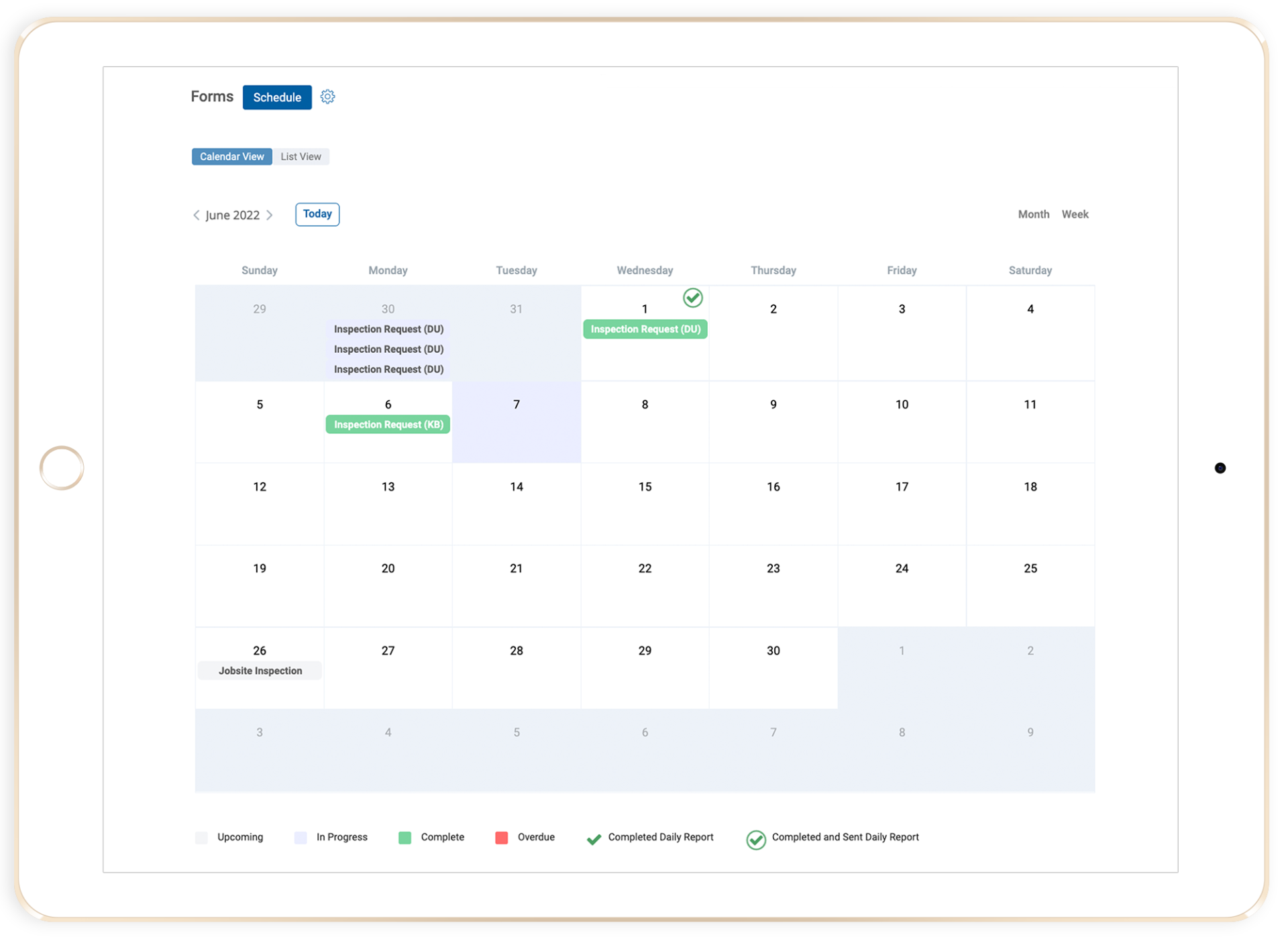
Busy superintendents and PMs are now handling forms much faster, saving McClone thousands of dollars in labor hours every year, Kanouff says. “But it’s not just the greater speed,” he added. “More of our paperwork is getting done simply because it is easier. People don’t put if off the way they might have when it was more labor-intensive.”
The ProNovos form-builder also makes it easy for subs to attach photos to inspection and other forms. The system automatically logs metadata, which can act as proof of compliance that goes beyond just a written description and a signature. On top of that, simultaneous publishing further improves compliance. Since construction jobsite safety forms change over time, when companies have multiple stakeholders across their different projects, those older approaches to handling forms can lead to some team members “not getting the memo.”
But the form-builder puts revisions into everyone’s hands simultaneously: As a new revision is made, from that point forward everyone has the update. In addition, ProNovos makes it easy to share construction jobsite safety forms with internal and external stakeholders via group email distributions. If you need to share a static document, any ProNovos custom form can be converted into an email- and printer-ready PDF file.
HIGHER-RESOLUTION PERSONNEL DATA
According to Kanouff, ProNovos has made it far easier for decision-makers at McClone to determine whether to crew up or crew down from week to week. They might use the system to find out if a particular superintendent is over-allocated during a certain timeframe, or look to see how many hours an engineer aims to spend on a specific project on a given date. “You want the right person for the right job,” he said. “By giving us greater transparency into our resources, ProNovos really helps us gauge and understand our active projects.”
In the same way as users update their “status” on social media, McClone’s teams use Operations Manager to quickly refresh key information. Whether sitting at a laptop in the office or swiping through a tablet in the field, decision-makers at McClone can access data related to overhead, materials, bids, costs, active projects, workloads, equipment and more at varying levels of detail. The system allows McClone to evaluate present and future workloads of key managers, superintendents and engineers at a glance.
“That’s a capability we haven’t seen in any other program,” Kanouff noted. “You can assign team members to certain jobs, put tasks against those personnel and ‘heat up’ their resource value.” Construction pros often juggle multiple projects; the ratings system helps McClone optimize its teams’ performance. For example, if a project manager ranks at or near full capacity, the company might assign an assistant to provide some additional boots on the ground. “Our teams are now better able to understand the work they’re taking on, which ensures that we make better business decisions,” Kanouff said. “We can gauge both the crew sizes and the resources that we have on our projects. It’s all embedded right in the application.”
“
That’s a capability we haven’t seen in any other program. Our teams are now better able to understand the work they’re taking on, which ensures that we make better business decisions.
Mikeal Kanouff
Area Manager, McClone
“
That’s a capability we haven’t seen in any other program. Our teams are now better able to understand the work they’re taking on, which ensures that we make better business decisions.
Mikeal Kanouff
Area Manager, McClone
CONSTRUCTION EQUIPMENT TRACKING
Subcontractors often struggle with construction equipment tracking. And yet when it comes to staying on schedule and on budget, knowing when and where a particular trencher or backhoe will be at a given time is important. In worst-case scenarios, subs shell out thousands of dollars in unnecessary rental costs: Concerned that a key piece of equipment will not be available for transfer to another jobsite at the right time, they sign a contract to rent another one for three or six months. In other cases, inadequate equipment forecasting creates costly delays on multiple job sites. “If you have 10 or 15 different jobs going on and everyone requests the same equipment at the same time, the result can be a problematic bottleneck,” Kanouff notes.
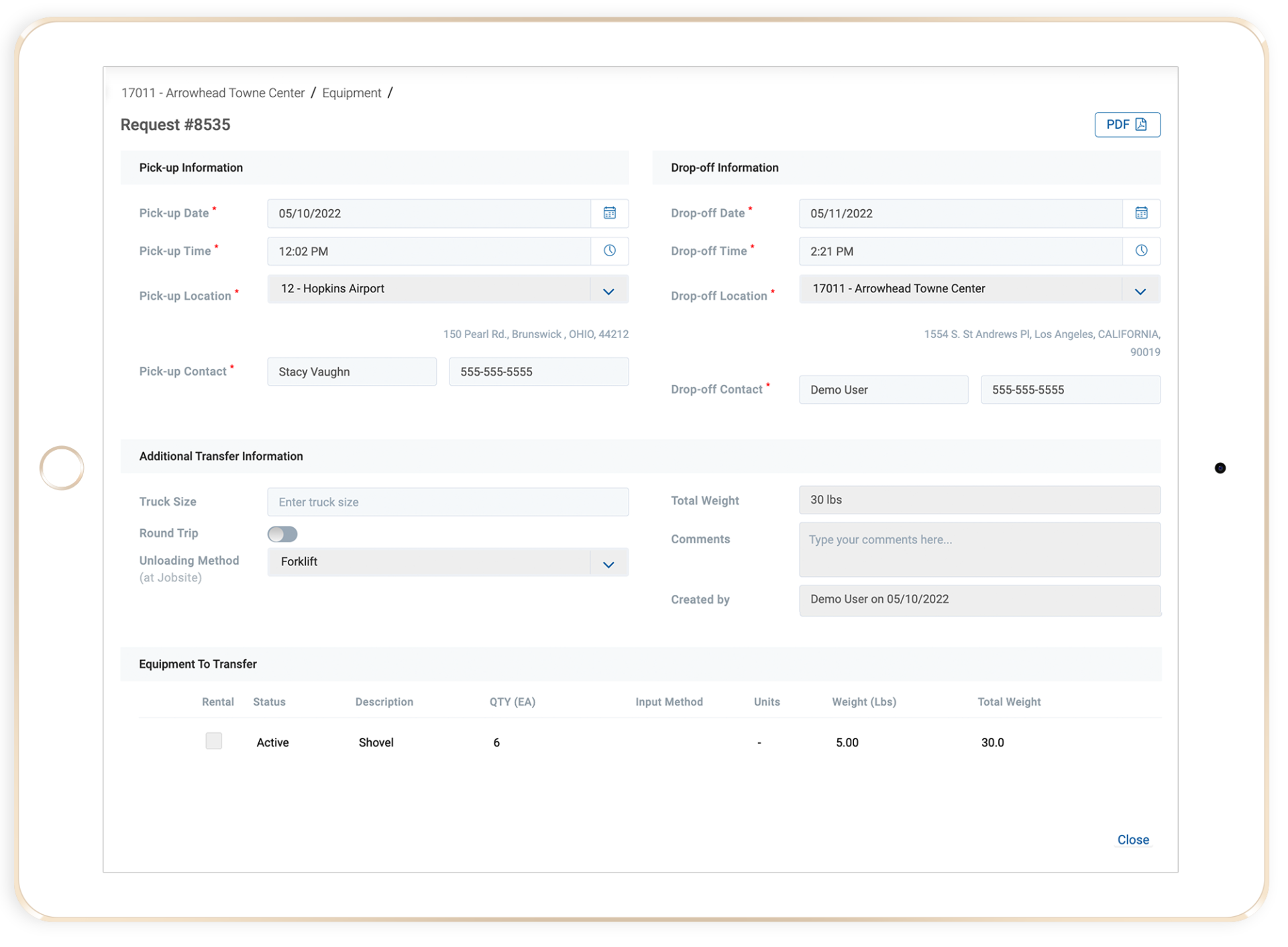
Having tried various apps and spreadsheet-based approaches to construction equipment tracking, McClone worked with ProNovos to implement a more efficient system. Simply by launching the app, McClone’s team members can now track and follow equipment wherever it is. “If I have a forklift that has a particular ID and I want to see where that forklift is, I can find it right away,” Kanouff said. The different parts of the system also talk to each other: When a team member successfully requests a given piece of equipment for a certain time period, that equipment no longer registers as available in the system.
The shift to more efficient construction equipment tracking has saved McClone tens of thousands of dollars in rental costs since switching to ProNovos. “There’s no need to spend money on rental equipment when the information is right there in the system,” Kanouff said. “We’re also using Operations Manager to gauge whether we want to continue to rent equipment or just make a capital expense and buy it.”
“
There’s no need to spend money on rental equipment when the information is right there in the system. We’re also using Operations Manager to gauge whether we want to continue to rent equipment or just make a capital expense and buy it.
Mikeal Kanouff
Area Manager, McClone
“
There’s no need to spend money on rental equipment when the information is right there in the system. We’re also using Operations Manager to gauge whether we want to continue to rent equipment or just make a capital expense and buy it.
Mikeal Kanouff
Area Manager, McClone
DATA-DRIVEN BIDDING AND PROJECT PRIORITIZATION
McClone also uses a ranking system to optimize the bidding process. In ProNovos, the contractor assigns a “1” ranking to estimated projects under negotiation, a “2” to those jobs it most wants to pursue and a “3” for estimated projects that are still uncertain. The rankings are based in part on how well present and future project resources align.
This approach has allowed McClone to avoid misallocating its resources—a capacity that is particularly important in hot construction markets or those in which the company maintains smaller offices. “Operations Manager helps them determine which projects to pursue,” Kanouff explained.
Transparency also helps during negotiations with customers. For any construction client, finding the right subcontractor is a critical consideration. ProNovos allows McClone to show prospects that it has quantified all resources needed for the job. “Customers appreciate knowing that you can back up your promises with carefully compiled and analyzed data,” Kanouff said.
“
Customers appreciate knowing that you can back up your promises with carefully compiled and analyzed data.
Mikeal Kanouff
Area Manager, McClone
“
Customers appreciate knowing that you can back up your promises with carefully compiled and analyzed data.
Mikeal Kanouff
Area Manager, McClone
DATA ANALYTICS AND NEW INSIGHTS
In addition to resource management, McClone also uses ProNovos to run analytics on its projects and operations. “We’ve been using historical data to run reports on things like equipment costs or jobs with similar characteristics. It has yielded valuable insights for us,” Kanouff noted.
With offices around the country, McClone also values the way individual teams can use ProNovos to self-manage their resources. “You can track, manage and analyze your resources by individual area, not just the entire company,” Kanouff explained.